Production and Capacity Planning Software
Increasing supply chain complexity and proliferating SKUs strain systems (and planners), leading to inaccurate plans and forecasts that don’t align with customer demand. ToolsGroup production planning software provides the visibility, insight, and control needed to improve planning efficiency and accuracy. It takes all resources and restrictions into account, from suppliers to all phases of production, leading to more optimal plans with less stress. Unlike systems that address only parts of the manufacturing process, our production planning solution orchestrates and optimizes the entire production operation.
Orchestrate and optimize the entire production planning lifecycle
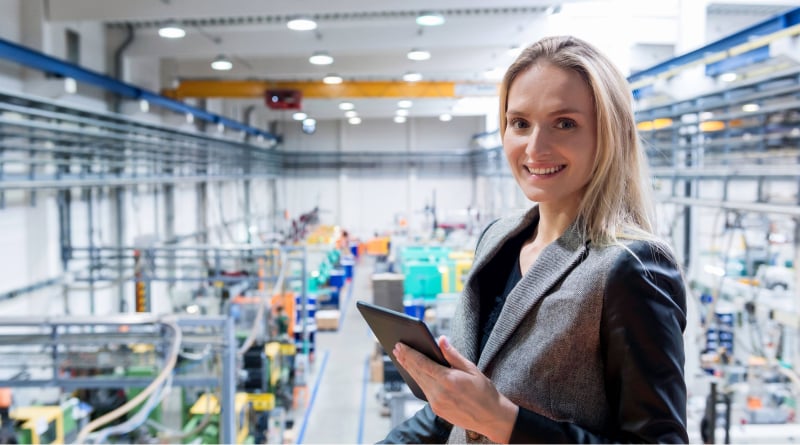
Increase production productivity and service levels
By creating more accurate plans and better capacity utilization, production planning software provides advanced planning insights that can improve productivity by 5-20% and help increase service levels.
Accelerate throughput and reduce inventory
Optimized production sequences and increased manufacturing efficiency can decrease throughput time by 15-30% and inventory levels by 10-20%.
Improve visibility into production
Master production planning and scheduling are combined into one single plan, improving visibility into production operations across the organization. Providing a better overview of the production plan — and the impact on both customer demand and orders — simplifies both the production process and sales operations planning.
Planners also enjoy less troubleshooting of production issues, with no need for detailed order-level analysis.
Reduce COGS
By increasing planner efficiency, improving the productivity of the manufacturing process, and reducing inventory levels, production planning software lowers the cost of goods sold (COGS).
In addition to the lower production costs, planning teams are better able to ensure the optimal inventory level thanks to quicker production order response times.
Elevate production planner productivity
Improved production planning gives operations management and planning teams increased visibility into a variety of manufacturing areas, including material requirements, available resources, and production planning bottlenecks.
Increased production control and reduced manual scheduling enable planners to manage greater complexities and have time freed up for exception handling and other tasks.
We went from a time-consuming manual planning to full focus on optimizing. Now we can plan even further ahead and our next goal is to get a GPS function for planning. We will tell it where we want to go and it will draw the map."
Peter Neiderud,
Director Supply Chain and QE
- Optimized production sequences
- Increased overall production planning efficiency
- Increased product availability
Production planning software features
Rules-based heuristics
These heuristics cover all planning restrictions in one step, considerably reducing the time needed to produce an accurate plan. The increased efficiency for manufacturing management teams helps ensure a seamless — and more profitable — production process.
High-performance finite capacity planning
Generate a production schedule in seconds, even for very complex manufacturing environments with huge amounts of data. The intuitive graphical interface lets management make production scheduling changes with just a few clicks. Precise modeling allows planners and manufacturers to forecast demand and easily simulate and compare alternative “what-if” production plan scenarios.
Production and supply chain planning
The enterprise resource planning system supports both procurement and production planning. Customer demand for finished goods is factored in to accommodate different scheduling approaches including make-to-stock, make-to-order, and assembly-to-order. The software also addresses medium to long-term planning, offering insight into long-term demand feasibility.
The Master Production Schedule (MPS) links sales and operations planning to logistics, taking demand forecasts into account when planning production and stock levels. It assesses available production capacity and calculates materials and resources needed to fulfill the production plan.
Manufacturing execution system (MES) integration
Connection with MES brings visibility to all steps in the production cycle, supporting production schedule dispatching, data collection and resources monitoring, shop-floor control, lot tracking and traceability, quality control plans management, label printing, plant maintenance, and KPI analysis.
MES also collects production line and shop-floor data through a range of devices, direct machine connections, and integrations with dedicated measuring and weighing systems.
Supplier connections
A simple web browser interface enables subcontractors and suppliers to easily share information that improves supply chain planning.
If production management is faced with shortages or restraints surrounding raw material requirements, improved communication with suppliers helps quickly identify the production issue, enabling planners to seek other available resources.